If you're looking for the best end mills for aluminum, it's important to understand the factors that determine their performance. Aluminum, being a soft metal, requires end mills that can quickly remove material without causing excessive wear and tear. But with the plethora of options available in the market, it can be difficult to choose the right one.
Firstly, choose an end mill with a high helix angle, as this will ensure that the chips are efficiently evacuated from the cutting zone, resulting in minimal heat buildup and longer tool life. Secondly, consider the coating on the end mill. A coating such as titanium nitride (TiN) or aluminum titanium nitride (AlTiN) can significantly improve its wear resistance. Finally, look for an end mill with a geometry optimized for aluminum such as a variable flute length, which can increase rigidity, reduce chatter, and enhance finish quality.
When it comes to selecting the best end mill for aluminum, questions like, “What is the ideal cutter diameter for my workpiece?” and “What flute count is best?” become important. Some manufacturers offer high-performance end mills that are specific for certain aluminum alloys. It’s essential to understand the difference between HSS (high-speed steel) and carbide end mills for aluminum, their strengths, and limitations. Knowing the RPMs (revolutions per minute) and feeds that can be used with aluminum end mills is critical for achieving a balanced material removal rate, tool life, and surface finish. By considering these factors, you’ll be well on your way to making the right choice for your specific aluminum milling application.
10 Best End Mills For Aluminum
# | Product Image | Product Name | Product Notes | Check Price |
---|---|---|---|---|
1
|
This product is ideal for milling aluminum using a 3-flute carbide end mill set ranging from 1/8-1/2.
|
|
||
2
|
This end mill is ideal for cutting hard and tough materials such as alloy steels and hardened steels.
|
|
||
3
|
The product is ideal for roughing and finishing aluminum applications with its high feed, U-Type design and 3 flute.
|
|
||
4
|
This product is ideal for cutting aluminum and other non-ferrous metals using a CNC router or mill.
|
|
||
5
|
Ideal for milling aluminum, regular length, 3 flute, 45-degree helix, uncoated finish, square end, 1/2" diameter.
|
|
||
6
|
Ideal for cutting aluminum and non-ferrous materials using a CNC machine, with an extra long 4 inch shank.
|
|
||
7
|
This product is ideal for roughing cuts on aluminum with its 3 flute, 42 degree helix design and long length.
|
|
||
8
|
It is ideal for cutting aluminum and other non-ferrous metals on a CNC machine.
|
|
||
9
|
The product is ideal for milling and cutting with high-speed steel and coated end mills in various sizes.
|
|
||
10
|
This product is ideal for milling machines and creating precise cuts on various materials with its titanium nitride coating.
|
|
1. Rip Cutting Tools 6 Piece 3-Flute Se Carbide End Mill Set For Aluminum, 1/8-1/2
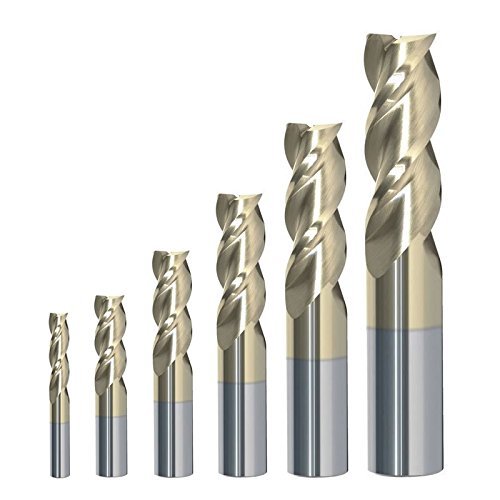
The Solid Carbide End Mill is a precision tool designed to meet the demands of professionals and DIY enthusiasts alike. With its ZrN coating, it is specifically designed for use on aluminum, providing superior wear resistance and extended tool life.
Featuring a 45-degree high helix, this end mill is capable of producing smooth, clean cuts with minimal chatter and reduced deflection. This allows for faster feed rates and increased productivity, making it an excellent choice for high-speed machining applications.
Each end mill is made in the USA with high-quality solid carbide, ensuring exceptional durability and performance. Its precise design and construction make it ideal for a wide range of milling tasks, from roughing to finishing.
With its superior quality and performance, the Solid Carbide End Mill with ZrN Coating is an essential tool for any professional or DIY enthusiast working with aluminum. Its precise design and construction make it an excellent choice for a wide range of milling tasks, providing exceptional results every time.
2. Taiwanese Carbide Square End Mills For Hardened Alloys.
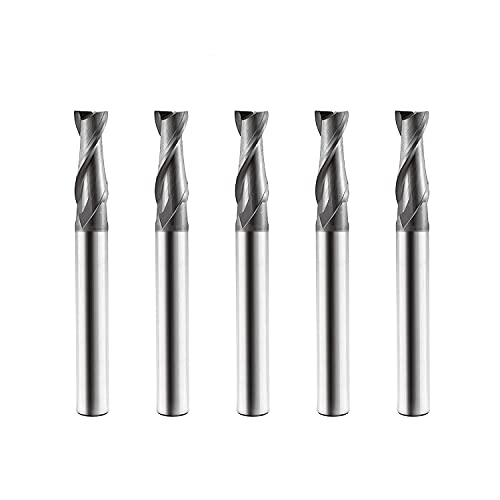
The Speed Tiger 600 Nano carbide cutter is a versatile tool that is perfect for cutting a wide range of materials, including carbon steels, alloy steels, pre-hardened steels, and cast iron. This cutter is made from micro-grain carbide, making it incredibly tough and resistant to wear. It offers exceptional cutting performance, even on hard materials like hardened steels with a hardness of HRC40-45.
One of the key features of this cutter is its AlTiBN coating. This coating is made from titanium aluminum boron nitride, which provides superior lubrication and wear resistance at high temperatures and cutting speeds. It is much more heat resistant than other coatings like TiAlN, TiN, or TiCN, making it an excellent choice for high-performance cutting applications.
The flutes on this cutter are ground by a world-class ISO-9001 factory, ensuring high-quality performance at a competitive price. This cutter is designed to deliver excellent results with minimal effort, making it a great choice for both professionals and DIY enthusiasts.
If you need help getting the best performance from your Speed Tiger cutter, you can rely on dedicated support from the seller. Simply contact them via Amazon at any time for cutting condition data and other helpful tips. Whether you're cutting carbon steel, alloy steel, pre-hardened steel, or cast iron, the Speed Tiger 600 Nano carbide cutter is a reliable tool that will get the job done with ease.
3. Aluminum Alchemist: High-Feed Carbide End Mill
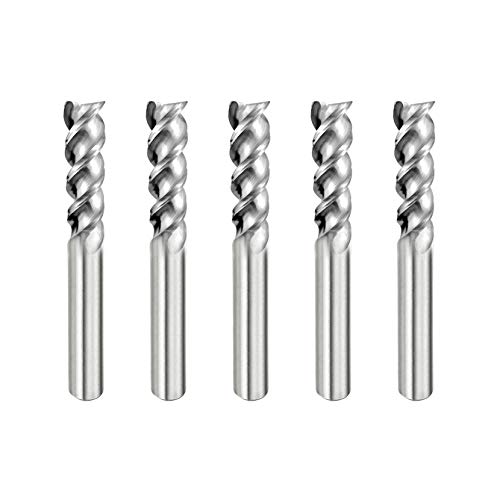
This high-performance cutter is designed to increase material removal rate (MRR), making it ideal for slotting applications. Its high feed U-type design makes it an excellent choice for working with aluminum and copper alloy materials. The cutter features a strong tooth with double relief angles, which improves tooth hardness and allows for excellent production rates.
The tooth design is optimized for alloys, ensuring that surface finishes are greatly improved, whether roughing or finishing. Additionally, effective chip removal is ensured thanks to the tooth design, further enhancing surface finishes.
This cutter is manufactured to the highest quality standards, with its flutes ground by a world-class ISO-9001 factory. With its superior design and construction, this cutter is an excellent choice for those in need of a high-performance cutter for aluminum and copper alloy applications.
4. Aluminum Router Bits – Cnc Spiral 3 Flutes
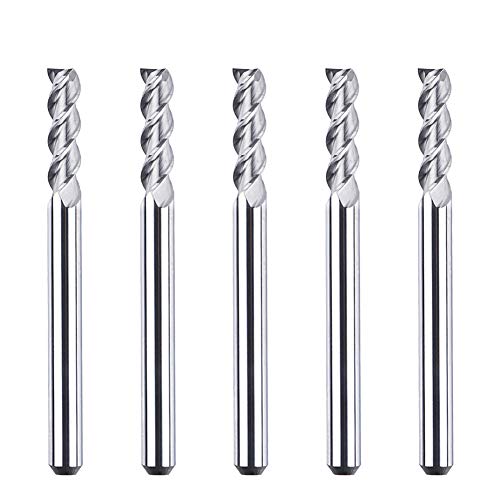
The end mills for aluminum are a versatile and high-quality set of cutting tools that are designed to provide superior performance and precision in aluminum processing. These end mills feature a 1/8” shank, 1/8” cutting diameter, 7/16” cutting length, and 1-1/2” total length, with 3 flutes and a flat top. The set includes 5 pieces, making it a great value for those who need a reliable and durable set of end mills.
One of the key features of these end mills is their high performance. They are designed to provide a perfect surface finish thanks to their effective chip removal, making them ideal for side milling, end milling, and finish machining. They also have a long service life, which means they can be used for a wide range of applications without needing to be replaced frequently.
Another important feature of these end mills is their high precision. They are made with high precision grinding and polishing techniques, which gives them high resistance to abrasion and temperature resistance. They are also highly rigid and durable, making them less likely to break during use.
These end mills are specifically designed for aluminum applications, and they work best with aluminum 6061 and 7075. However, they are also suitable for use with non-ferrous metals, plywood, OAK, MDF, and any hardwood working. This makes them a versatile set of end mills that can be used for a wide range of projects.
Finally, these aluminum end mills are widely used and are compatible with a variety of routers. They are suitable for use with CNC routers, as well as with Makita, Bosch, or any brands of plunge routers with a 1/8" collet. This makes them a great choice for anyone who needs a reliable set of end mills for their workshop.
5. Alu-Power Carbide End Mill – 3/8" Square.
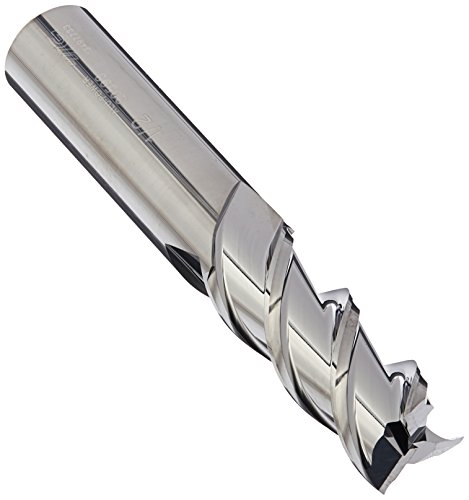
If you're looking for a high-quality milling tool for non-ferrous materials such as aluminum, look no further than this expertly crafted option. With its advanced design and top-of-the-line features, this milling tool is perfect for achieving precision cuts at high speeds.
One of the key advantages of this milling tool is its three-flute and 45° helix design, which helps to maintain harmonic balance even at high speeds. This means that you can achieve smooth, consistent cuts without worrying about vibration or other issues that can negatively impact the quality of your work.
In addition to its advanced design, this milling tool also boasts a tightly controlled cylindrical margin that helps to improve surface roughness and ensure a clean, precise cut every time. And with its maximum-metal removal rate, you can work quickly and efficiently without sacrificing quality or accuracy.
Finally, this milling tool also features superior chip evacuation capabilities, which help to prevent clogs and other issues that can slow down your work and reduce the quality of your results. With all of these features and more, this milling tool is the perfect choice for anyone looking to achieve professional-quality results with non-ferrous materials.
6. Extra Long Aluminum Cnc Cutting Bit
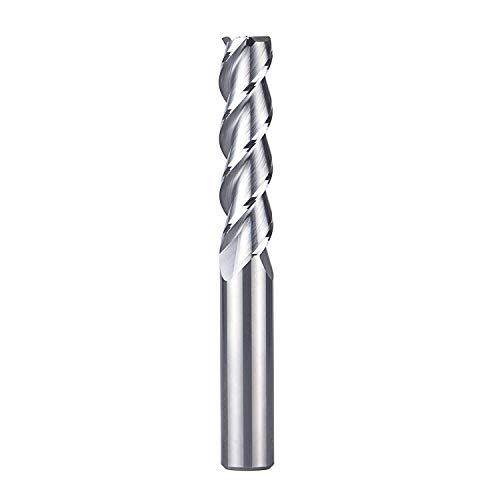
This Solid Carbide Spiral Router Bit is a versatile tool that is designed to deliver high-quality results for a wide range of woodworking applications. With a 1/2 inch shank and 1/2 inch cutting diameter, this router bit is perfect for achieving precise cuts with ease. It has a 2 inch cutting length and a total length of 4 inches, making it suitable for a variety of cutting depths.
The router bit features a flat top with a 3-flute design that ensures easy chip removal and a perfect surface finish. The clockwise motion of the bit makes it ideal for machining a variety of materials, including aluminum 6061, 7075, non-ferrous metals, plywood, oak, MDF, and any hardwood.
This carbide end mill is suitable for use with a CNC router, as well as Makita, Bosch, and any brand plunge router with a 1/2" collet. Its long service life ensures that it stays sharp even after prolonged use, making it an ideal tool for both professionals and DIY enthusiasts.
The end mill bits are suitable for side milling, end milling, finish machining, and other applications. They are designed to deliver high performance and precision to ensure that every project is completed to the highest standards.
7. Speedy Alum Rougher: Yg-1 End Mill
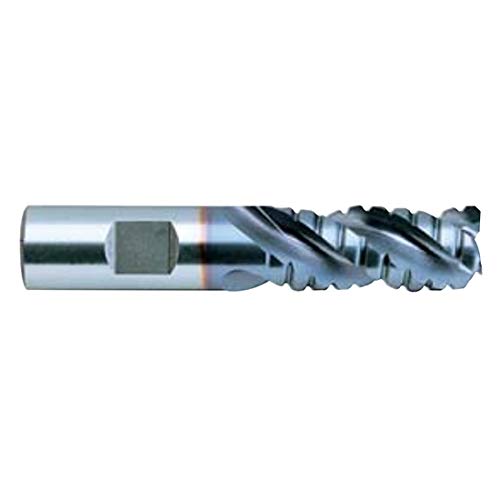
This aluminum alloy metal removal tool boasts of high performance and is designed to deliver impressive results. The tool is manufactured in South Korea, a country known for its high-quality products. The package dimensions are compact and easy to store, measuring 3 inches in length, 1 inch in width, and 1 inch in height.
Users can expect exceptional metal removal capabilities when using this tool on aluminum alloys. The high-performance design ensures that the tool can handle tough jobs with ease, making it ideal for professionals who require reliable and efficient equipment.
With its compact size, the tool is easy to handle and maneuver, allowing users to work on intricate parts and surfaces with precision. The tool's design also ensures that it is durable and long-lasting, making it a valuable addition to any metalworking toolkit.
Whether you are a professional metalworker or a DIY enthusiast, this aluminum alloy metal removal tool is an excellent investment. Its high-performance capabilities, combined with its compact size and durable design, make it an ideal tool for any metalworking project.
8. Spiralmax Aluminum Cnc Router Bit
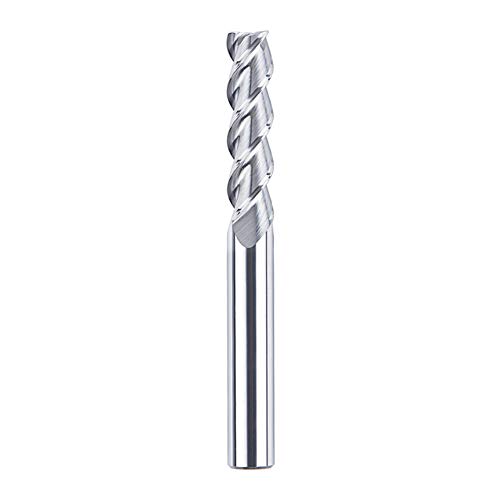
Looking for a router bit that can handle a variety of materials and provide a perfect surface finish? Look no further than the Solid Carbide Spiral Router Bit with a 3/8 inch shank and cutting diameter, a 1-1/2 inch cutting length, and a total length of 3-1/2 inches.
Featuring a flat top and 3-flute design, this router bit is perfect for easy chip removal and a smooth surface finish. It also offers a clockwise motion for machining, making it a versatile tool for any project.
Designed for use with non-ferrous metals like aluminum 6061,7075, as well as plywood, oak, MDF, and any hardwood, this carbide end mill boasts a long service life for sharp and precise cuts. It is also compatible with CNC routers and plunge routers from top brands like Makita and Bosch that have a 3/8" collet.
Whether you need to side mill, end mill, or finish machine, this end mill bit can handle the job with ease. Its solid carbide construction ensures durability and reliability, while its spiral design allows for a smoother cutting action.
Invest in the Solid Carbide Spiral Router Bit for a high-quality tool that will help you achieve professional results on a variety of materials.
9. Accusize 20pc End Mill Set – Tin Coated
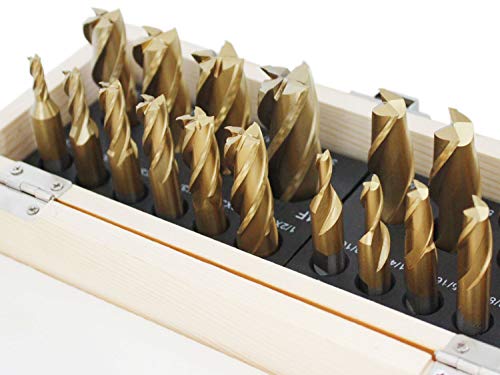
This set of drill bits is a must-have for any serious DIY enthusiast or professional. Made from high-speed steel and coated with Tin, these drill bits are built to last and perform to the highest standards. The straight shank design ensures that the bits fit securely into any drill chuck, providing maximum stability and precision during use.
The set includes one of each size in both 2 and 4 flute variations, covering a wide range of applications. The 3/8-inch shank sizes include 3/16-inch, 1/4-inch, 5/16-inch, 3/8-inch, and 7/16-inch, while the 1/2-inch shank sizes include 1/2-inch and 9/16-inch. The set also includes 5/8-inch and 11/16-inch sizes with a 5/8-inch shank, and a 3/4-inch size with a 3/4-inch shank.
Thanks to their high-speed steel construction, these drill bits are able to withstand even the toughest materials, such as metal and hardwoods. The Tin coating adds an extra layer of protection, preventing rust and corrosion from damaging the bits over time. The straight shank design also allows for easy removal of the bits from the drill chuck, making it a breeze to switch between different sizes and types of bits.
10. 20 Pc Titanium Nitride Coated End Mill Set – 4 & 2 Flute Tin End Mill For Milling Machines
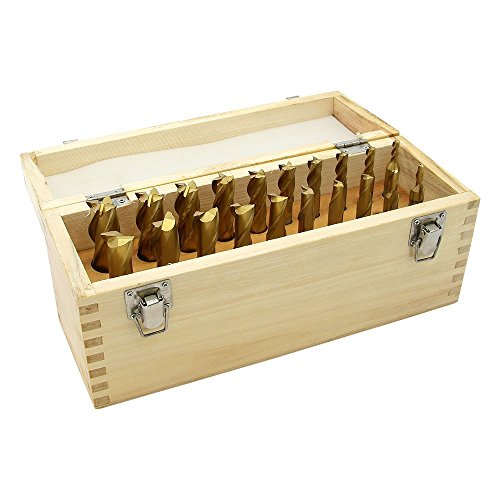
Looking for a set of high-quality end mills that can handle tough cutting tasks? Look no further than this comprehensive set, which includes both 10pc-2 flute and 10pc-4 flute end mills.
With sizes ranging from 3/16" to 3/4", and shank sizes from 3/8" to 3/4", this set is designed to tackle a wide range of milling tasks with ease. The end mills are made from M2 titanium nitride-coated high-speed steel, which makes them durable and long-lasting.
One of the standout features of this set is its center cutting capabilities. This means that the end mills are able to plunge into a workpiece and cut radially, rather than just cutting around the outside edges. This makes them ideal for tasks such as creating slots or pockets in your material.
All of the end mills come packaged in a custom wooden case, which measures approximately 10-1/4''L x 3-1/4''W x 4-1/2''H. This makes it easy to keep your end mills organized and protected when not in use.
Whether you're a professional machinist or a DIY enthusiast, this end mill set is sure to be a valuable addition to your tool collection. With its high-quality materials, versatile sizes, and center cutting capabilities, it's the perfect choice for anyone who needs to tackle tough milling tasks.
Best End Mills For Aluminum FAQs
How do carbide vs. HSS end mills compare for machining aluminum?
When it comes to machining aluminum, both carbide and high-speed steel (HSS) end mills are commonly used. However, there are some differences between the two that can affect their performance and suitability for specific applications.
Carbide end mills are harder and more wear-resistant than HSS end mills, making them more durable and longer-lasting. They are also able to withstand higher temperatures and are less prone to chipping or breaking. This makes them ideal for high-speed machining operations and for machining harder materials like aluminum alloys. Carbide end mills also typically have sharper cutting edges, which can improve surface finish and reduce cutting forces.
On the other hand, HSS end mills are generally less expensive than carbide end mills and can be a good choice for less demanding machining applications. They are also more ductile than carbide, which can make them less prone to breaking or chipping in certain situations. However, HSS end mills may not last as long as carbide end mills and may not be suitable for high-speed machining operations or for machining harder materials.
Overall, the choice between carbide and HSS end mills for machining aluminum will depend on the specific application and the desired balance between performance and cost. Carbide end mills are generally the preferred choice for high-speed machining operations and for machining harder materials, while HSS end mills may be a good option for less demanding applications where cost is a factor.
How do different end mill geometries affect performance when machining aluminum?
End mill geometries play a critical role in determining the performance of the cutting tool when machining aluminum. The choice of geometry depends on various factors such as the type of aluminum alloy, cutting speed, feed rate, and depth of cut.
For instance, a flat end mill geometry is ideal for roughing operations in aluminum because it has a large cross-sectional area that can remove a lot of material quickly. On the other hand, a ball nose end mill is perfect for finishing operations in aluminum because it has a rounded tip that can create smooth surfaces without leaving any marks or burrs.
Another important factor is the number of flutes on the end mill. A high number of flutes can improve the surface finish, but it can also increase the risk of clogging and chip evacuation. Therefore, a balance between flute number and cutting speed is necessary to achieve optimal performance.
In summary, choosing the right end mill geometry for machining aluminum depends on several factors, and it requires careful consideration of the material, the cutting parameters, and the desired outcome. By selecting the appropriate geometry, machinists can achieve high-quality results with minimal waste and tool wear.
How do different end mill materials, such as cobalt and carbide, compare for machining aluminum?
When it comes to machining aluminum, the choice of end mill material can significantly impact the efficiency and quality of the process. Cobalt and carbide are two of the most commonly used materials for end mills, and they have distinct differences in performance.
Cobalt end mills are known for their toughness and ability to resist wear and heat. They are ideal for cutting through tough materials like stainless steel and high-temperature alloys. However, when it comes to aluminum, cobalt end mills may not be the best option. They tend to generate a lot of heat when cutting aluminum, which can cause the material to melt and stick to the end mill, resulting in poor surface finish and reduced tool life.
On the other hand, carbide end mills are highly recommended for machining aluminum. They are much harder than cobalt and can withstand high cutting speeds and temperatures without losing their cutting edges. Carbide end mills also produce less heat and generate less friction when cutting aluminum, which results in better surface finish and longer tool life.
In summary, while cobalt end mills are ideal for tough materials, carbide end mills are the preferred choice for aluminum machining due to their hardness, resistance to wear and heat, and ability to produce high-quality surface finishes.
How do high helix end mills perform when machining aluminum?
High helix end mills are known for their ability to remove material quickly and efficiently, making them a popular choice for machining aluminum. The high helix angle allows for a larger chip load, which means more material can be removed with each pass. This can result in faster machining times and reduced tool wear.
One of the main advantages of using high helix end mills for aluminum is their ability to prevent chip buildup. The larger flute spacing and higher helix angle help to evacuate chips more effectively, reducing the likelihood of chip recutting and improving surface finish.
It is important to note that the performance of high helix end mills can vary depending on the specific application and the material being machined. Factors such as spindle speed, feed rate, and depth of cut can all affect the performance of the tool. Additionally, it is important to choose the right coating for the end mill to ensure maximum tool life and performance.
What are some of the best brands for end mills used for aluminum?
When it comes to end mills used for aluminum, there are several brands that are highly recommended by professionals in the industry. One of the top brands is Harvey Tool, which offers a wide range of end mills specifically designed for aluminum machining. Their products are made with high-quality materials and advanced manufacturing techniques, ensuring consistent performance and long tool life.
Another popular brand is OSG, which offers a variety of end mills for aluminum machining, including their EXOCARB line. These end mills are designed with a unique geometry that provides excellent chip evacuation and reduced cutting forces, resulting in smoother cuts and longer tool life.
Other reputable brands for end mills used for aluminum include Kennametal, Niagara Cutter, and Emuge. These brands offer a range of options for different cutting applications and budgets, so it's important to do your research and choose the one that best fits your needs.
Ultimately, the best brand for end mills used for aluminum will depend on your specific machining requirements and preferences. It's always a good idea to consult with a knowledgeable supplier or industry expert before making a purchase to ensure that you're getting the right tool for the job.
What are the most important factors to consider when selecting the best end mills for aluminum?
When selecting the best end mills for aluminum, there are several important factors to consider for optimal performance.
Firstly, the material of the end mill is crucial. Carbide or diamond coatings are ideal for aluminum as they provide high hardness and durability, allowing for longer tool life and better surface finish.
Secondly, the type of end mill is important. A high helix angle and variable flute design can provide better chip removal and reduce the risk of chip packing, which is a common issue when machining aluminum.
Thirdly, the coating on the end mill is critical. A coating such as TiAlN or TiCN can provide high wear resistance and reduce the risk of built-up edge, which is important when machining softer materials like aluminum.
Finally, the cutting parameters such as speed, feed, and depth of cut should be carefully selected based on the specific application and material being machined. Optimal cutting parameters can reduce the risk of tool breakage and achieve the desired surface finish.
Overall, selecting the best end mills for aluminum requires careful consideration of the material, type, coating, and cutting parameters for optimal performance.
What is the best cutting speed and feed rate for aluminum end mills?
The best cutting speed and feed rate for aluminum end mills depend on various factors such as the type of aluminum, the size and geometry of the end mill, and the type of machine being used. Generally, for soft aluminum alloys, the recommended cutting speed ranges between 500-1,000 surface feet per minute (SFM), while the ideal feed rate is around 0.003-0.005 inches per tooth (IPT). For harder aluminum alloys, the cutting speed should be reduced to around 200-400 SFM, while the feed rate can be increased to 0.005-0.008 IPT. It is crucial to note that cutting speed and feed rate are interrelated, and adjusting one without considering the other can negatively impact the end mill's performance. Therefore, it is recommended to follow the manufacturer's guidelines and optimize the cutting parameters based on the specific application requirements. Additionally, using proper cooling and lubrication techniques can help improve the end mill's performance and prolong its lifespan.
What size and flute count are optimal for end mills used for aluminum?
When it comes to end mills used for aluminum, the optimal size and flute count can vary depending on the specific application and requirements. However, there are some general guidelines that can help in selecting the right end mill for the job.
For aluminum, it is generally recommended to use smaller end mills with a diameter of 1/8" to 3/4". This is because aluminum is a softer material compared to other metals, and smaller end mills can provide better control and precision in cutting.
In terms of flute count, two or three flutes are typically recommended for aluminum. This is because fewer flutes can help to prevent the end mill from clogging with chips, which can be a common issue when machining aluminum. However, if a higher feed rate is required, four flutes can also be used.
It is important to note that the optimal size and flute count can also depend on other factors such as the depth of cut, spindle speed, and cutting tool material. Therefore, it is recommended to consult with a machining expert or manufacturer to determine the best end mill for the specific application.
What types of aluminum alloys are best suited for specific end mills?
The choice of aluminum alloy for end mills depends on various factors such as the alloy's composition, microstructure, and the machining conditions. Generally, aluminum alloys are classified into two categories: wrought alloys and cast alloys. Wrought alloys are further classified into heat-treatable and non-heat treatable alloys.
For end mills, non-heat treatable alloys such as 1100 and 3003 are suitable for machining. These alloys are soft, ductile, and have good machinability. Heat-treatable alloys such as 6061 and 7075 are commonly used for high-speed machining. These alloys are harder and stronger, but they require special cutting tools and machining conditions.
The type of end mill also plays a role in selecting the appropriate alloy. For example, carbide end mills are suitable for machining hard alloys, while high-speed steel end mills are suitable for soft alloys. Additionally, the geometry of the end mill and the machining parameters such as cutting speed, feed rate, and depth of cut should be optimized for the specific alloy being machined.
In summary, the best-suited aluminum alloys for specific end mills depend on various factors such as the alloy's composition, microstructure, end mill type, and machining conditions.
What types of coatings are best suited for aluminum end mills?
Aluminum end mills are commonly used for milling aluminum and other non-ferrous metals. When it comes to coatings, the selection depends on the specific application and the cutting conditions. Generally, coatings on aluminum end mills are used to reduce friction, increase tool life, and improve surface finish.
The most common coatings for aluminum end mills include TiN (titanium nitride), TiCN (titanium carbonitride), and TiAlN (titanium aluminum nitride). TiN is a general-purpose coating that provides good wear resistance, while TiCN is suitable for high-speed machining due to its high hardness and thermal stability. TiAlN is the most preferred coating for aluminum end mills as it offers excellent hardness, toughness, and high-temperature resistance.
Other coatings such as ZrN (zirconium nitride) and DLC (diamond-like carbon) are also used for specific applications. ZrN provides good adhesion and hardness, while DLC offers low friction and high wear resistance. Ultimately, the selection of the coating depends on the specific application requirements, cutting speeds, and feed rates.